
Fatigue refers to the progressive damage of the material under cyclic loading and is one of the main reasons for the failure of mechanical components.
If the applied cyclic loading is high enough to plastically deform the material during each cycle, low-cycle fatigue regime is recalled and the elastoplastic material properties are particularly important.
In this work, the elastoplastic and low-cycle fatigue properties of a widely used wrought AISI 316L stainless steel were examined and modelled. Firstly, experimental tests were carried out to calibrate an elastoplastic cyclic model (i.e. Chaboche and Voce). Secondly, from the same test, material cyclic endurance (fatigue) was characterised as well.
If combined using an appropriate failure criterion, both the elastoplastic model and the fatigue properties can be used for the evaluation of real components life during the design stages and lead to more safe and reliable products. This can be attained by implementing the model in a commercial Finite Element-based code to account for the complexity of a real engineering problem.
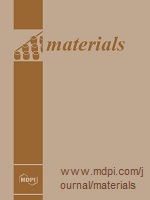
M. Pelegatti, A. Lanzutti, E. Salvati, J. S. Novak, F. De Bona, D. Benasciutti. Cyclic plasticity and low cycle fatigue of an AISI 316L stainless steel: experimental evaluation of material parameters for durability design (2021) Materials.